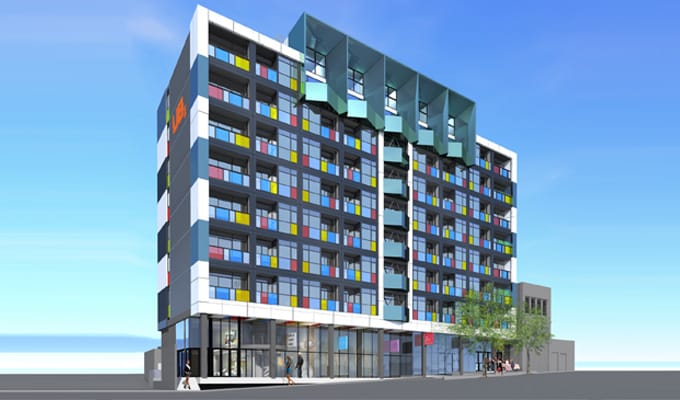
The construction industry is in the midst of disruptive change.
Prefabrication is on the rise. Also called off-site construction, prefab has become the preferred option for big-name developers such as Lend Lease, Brookfield and Mirvac on a variety of projects. The publicly listed global healthcare company, Ramsay Health Care, is using prefab to extend and build its hospitals.
It’s a big image change for prefab. Most of us associate prefab buildings with housing commission towers, mining towns or the portable classrooms we sweltered or froze in as kids. Unhappy memories.
Out and proud
Using prefabrication was once a guilty secret; developers that used prefab did not advertise the fact (many still don’t). But the Australian industry is proudly announcing itself as part of a worldwide trend.
In Europe, developers have publicly embraced prefab. Australia is joining them, and its prefab products are among the world leaders in quality, design and technology, says Damien Crough, the chair and founding director of the peak body, PrefabAUS.
Crough estimates that prefab represents about 3% of the $30b a year construction sector. He sees big growth in the next five years. “Our target is to see 10% of the building being prefab by 2020 – that is realistic,” he says. “NZ is over 10%. The US, UK and Japan, are 15-20%, and in Sweden and Finland, it’s up to 70%.”
More than 200 participants are expected at PrefabAUS’s second annual conference, scheduled for September 14-16 in Melbourne. Crough, who is the event facilitator, says last year’s inaugural conference was a sellout, with 30 people on a waiting list for tickets.
Excited about the growth prospects for the prefab sector, architects, engineers, developers and manufacturers are all members of PrefabAUS. They include big players, such as Sinclair Knight Mertz, Mirvac, Arup, and Norman Disney Young.
A new direction for Australian manufacturers
Beleaguered car and car-parts manufacturers are excited by the development of prefab; already auto-parts suppliers are transitioning from auto parts to building parts, and Crough believed many skilled workers from the auto industry will find new careers in the prefab building sector.
Crough says: “Composites Materials Engineering, maker of parts for Ford and Holden, is now making acrylic splashbacks and shower bases. Hella, which makes vehicle lighting, is expanding into architectural lighting.”
The car manufacturing research company, AutoCRC, partly funded under the Federal Government’s Cooperative Research Centres program, is a conference sponsor.
Banks: a barrier to expansion
Crough has been at the forefront of the transformation of prefab, joining architect Nonda Katsalidis’ company, Unitised Building, formed in 2007.
Katsalidis wanted to stabilise the construction costs of high-rise apartments. UB bought two sites to build demonstration projects; the first was an eight-storey apartment block called Little Hero in Melbourne’s city centre.
But when they took their projects to the banks, they hit a wall. The banks saw heightened risk with the new process. Arab Bank was the only one willing to back UB, and funded its first two projects.
Little Hero was a resounding success. The apartments were built in UB’s Brooklyn factory; the on-site construction time was four weeks. Subsequent projects went up even faster.
Off-site construction reduces costs, in particular, waste which is cut by up to 90%. It also cuts on-site disruption and noise and reduces the use of concrete, one of the worst contributors to greenhouse gas in the world.
All three factors give prefab outstanding green credentials.
But the banks remain a thorn in the side of the burgeoning prefab construction sector. Crough says: “They want particular assurances.”
Bank demands for interest rates and other assurances eat away at prefab’s competitive advantages.
Healthcare: A source of growth
Hospitals extensions will be a strong source of work in coming years, says Jan Gyrn, a founding director of Modscape, another long-standing player in the design and manufacturer of prefab buildings. “We made a decision to become active in the healthcare sector,” Gyrn says, but he says his healthcare clients prefer not to go public about using prefab construction.
For hospital patients it’s hard to tolerate the noise and disruption associated with on-site construction; hospitals are forced to close beds, losing tens of thousands every day. That makes off-site construction very attractive.
The Melbourne Zoo had similar noise concerns. One of Modscape’s early clients, the zoo managers didn’t want the animals disturbed by months of on-site construction that their new administration block would require. “We came along one day to install the building. There were no drop saws and hammers,” Gryn says. “We didn’t disturb the animals.”
Education is the imperative
Gyrn is also a founding director of PrefabAUS, as is Hickory Group, a company that initially funded and then bought Unitised Building’s factory. The two companies have factories across the road from each other in Melbourne’s inner west. Gyrn says his company now makes as much in a month as it did in its first year nine years ago.
But PrefabAUS has a big job to re-educate the conservative construction and banking sectors.
The group holds industry seminars and workshops every couple of months in its goal to:
- Redress the stigma of prefab.
- Demonstrate the design flexibility that architects want.
- Showcase projects.
- Reassure the bank and other funders.
- Win the support of regulators and policy-makers.
- Prove its benefits and green credentials.
- Interest developers and their clients in using some (if not all) prefab components in their constructions.
- Attract manufacturers to provide the parts.
Gyrn says: “Our objective is to try to promote the industry and lead by example. The key to successful building is often a mix of onsite and modular construction that is best suited for the type of building.”